July 28, 2022
How to Reduce Risk in the Construction Industry
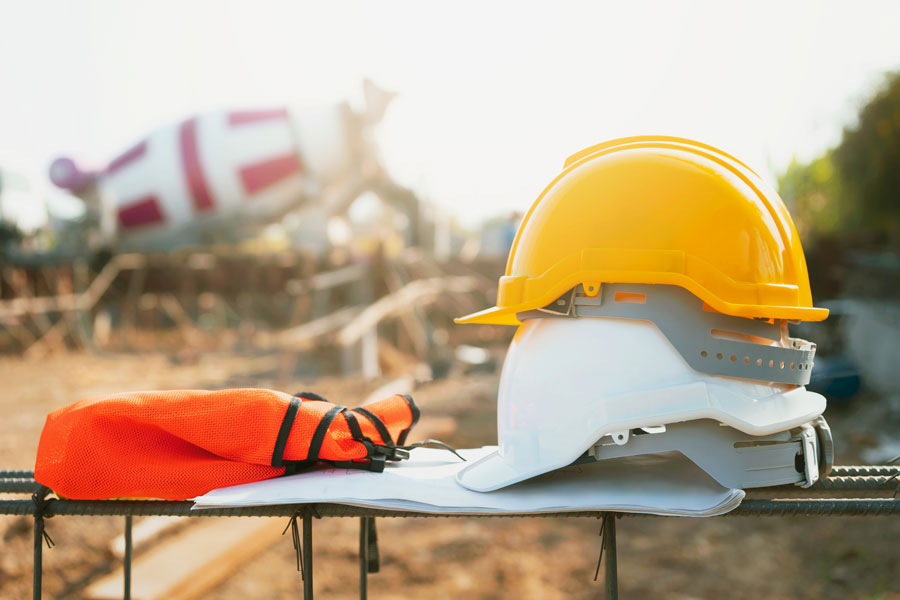
Recent technologies — from robotics to project management software — as well as better ways to identify and deal with risk are helping the construction industry save money and reduce accidents.
Workforce Shortage
COVID and its ramifications have placed a strain on finding good workers for most industries. This is no less true for construction. With the increased demand for skilled workers, some firms are adopting automated technologies for tasks like excavation, drywall installation, painting and roofing. Using robotics not only reduces labor costs but jobs can be completed faster since robots work night and day and don’t need regular shifts.
Construction Defects
Construction defects result from poor workmanship and errors and omissions. Poor workmanship occurs when the hired sub-contractors are just wrong for the job. Proper homework is the best remedy. Design defects result from architect and engineer errors, including errors in drawings and working documents. When design errors occur and change orders are needed, liability including additional costs incurred should be contractually transferred to the design professional. Use a knowledgeable insurance agent.
Contractual Risk
Hiring sub-contractors entails a fair degree of risk, which in general can be addressed by using precisely worded contracts, such as those that follow American Institute of Architects language. However, these clauses don’t necessarily protect you from the negative actions of subs (and their subs), they just provide a legal remedy after the damage occurs.
Your best course is to heed the advice published on the website Jobsite, paraphrased here: At the outset of any project, during the bid stage, spell out the team’s roles and responsibilities. Getting a list of all subcontractors and their subs at bid time gives you a chance to qualify them so you not only know who is working on the project, but also their qualifications, experience, and track records.
Site Protection
The website ForConstructionPros.com offers these tips:
- Increase lighting in off-hours
- Let employees know that the boss is paying attention
- Schedule supplies only as needed
- Keep good records with documentation
- Practice effective inventory management
- Secure perimeter with fencing
- Review security plan and process
- Use theft deterrents or cameras
Environmental Risks
Hurricanes happen, as do tornadoes, floods, fires and lightening storms. It’s hard to predict a natural disaster, so be prepared. Contaminants and other jobsite hazards are also environmental risks. Some potential hazards contractors should be aware of in order to mitigate risk include:
- Air emissions from chemicals, equipment or activities like welding and concrete cutting
- Spills from fuels or lubricants associated with construction equipment
- Release of asbestos particles from asbestos containing materials (ACM) such as insulation, floor tiles, or ceiling tiles
- Release of lead particles from lead-based paint
- Release of mold or mold spores from areas where water intrusion has occurred, such as broken pipes or inadequate drainage
- Releases of chlorofluorocarbons (CFC’s) in air conditioners or refrigeration units
- Spills of oil used, transferred or stored at construction sites
- Moving soil on or off-site that contains hazardous chemicals.
Managing Change Orders
These tips come from eSub, a construction management software vendor:
- Identify issues before you begin. Before starting the project, carefully examine the plans and specifications to identify any ambiguities or conflicts immediately. Putting in the extra time at the front end of a project to review the work, bid, drawings, and details can minimize change orders.
- Be transparent with stakeholders. Stakeholders need to stay informed. Always communicate any project changes and updates to prevent misunderstandings and save time.
- Verify how the change impacts the project. Change order disputes can greatly impact a project, especially if the work is put on pause while the parties dispute the change order. If not resolved as soon as possible, change order disputes can increase project delays and escalate costs.
Using construction management software can greatly streamline the process and make it more effective.
Documentation Organization
Proper document management is a tedious and time-consuming task. Construction projects require hundreds, sometimes thousands, of documents. Now that contractors are transitioning from paper to digital documentation accessing them can be streamlined. Construction software platforms use cloud-based technologies that allow instant document retrieval, reducing schedule delays and centralizing accessibility in one location.